Lookout For Anticipated 2019 ASME Code Changes
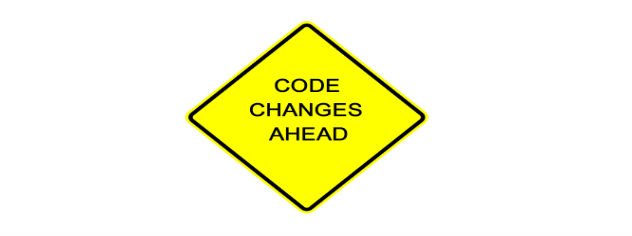
As the year progresses and new codes are published, there are a few things to keep a lookout for, particularly with respect to material property requirements. Two materials are of particular interest, and are reportedly likely to change with the 2019 edition of ASME Section VIII-1. The potential ramifications of these changes on pressure equipment […]
CRN Number Registration: Essential No. 1 Step
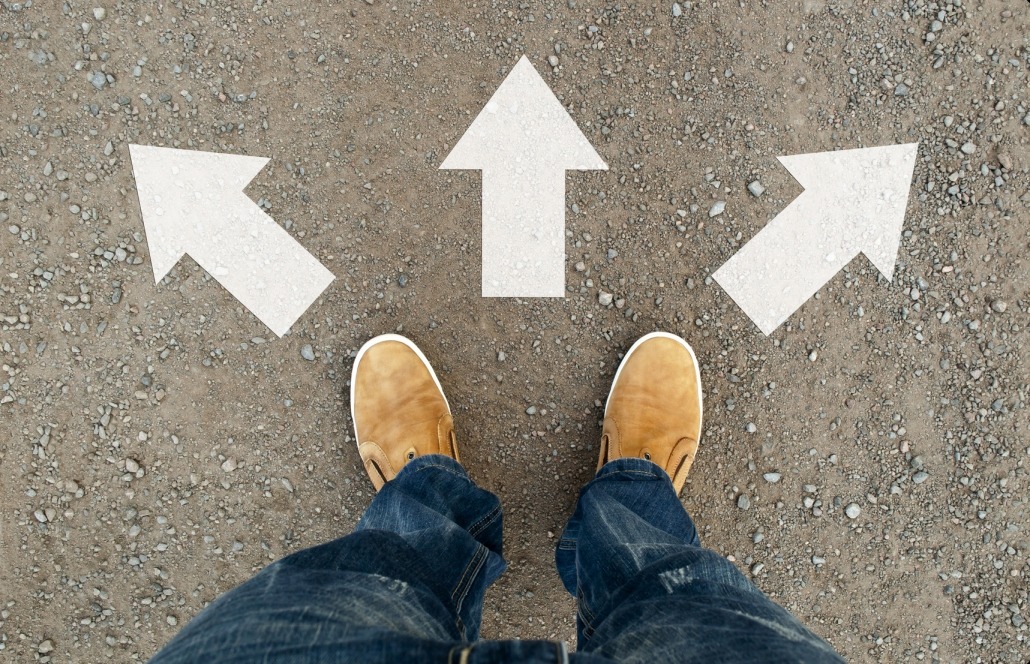
We continue to rapidly explain what is needed to properly design pressure equipment (vessels, boilers, fittings, piping systems) to get CRN number registration. Many designs proposed to us are deficient for the same obvious reason and consequences that stem from it. Surprisingly enough, even established and accredited pressure equipment manufacturers sometimes don’t even know the […]